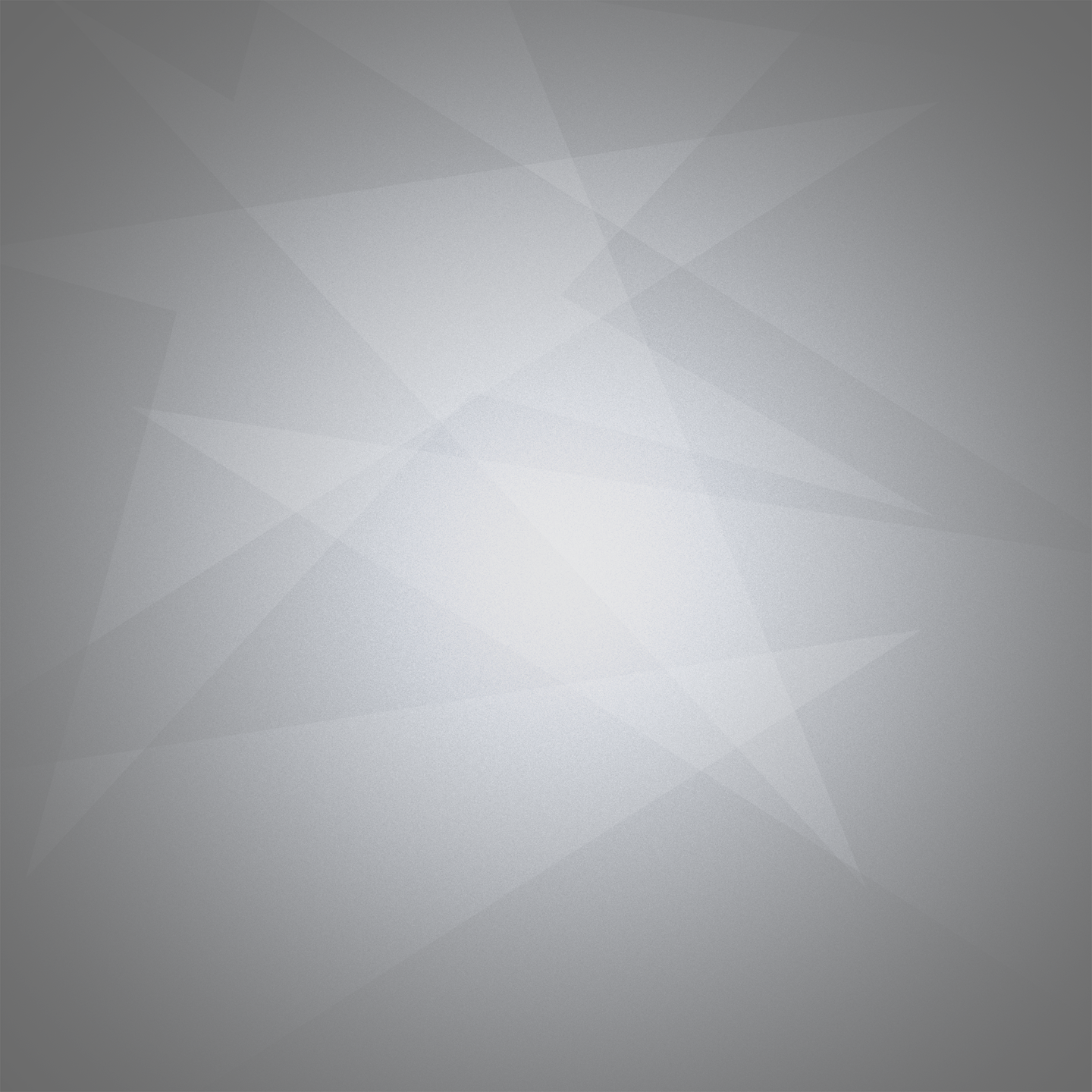

Engineering Applications
AME-5001
Group - II
Manufacturing Processes
Turning
This operation is one of the most basic machining processes. That is, the part is rotated while a single point cutting tool is moved parallel to the axis of rotation. Turning can be done on the external surface of the part as well as internally (boring). The starting material is generally a workpiece generated by other processes such as casting, forging, extrusion, or drawing.
Taper Turning
A job which decreases in diameter gradually so that it assumes a conical shape is said to be tapered. Taper angle is the angle, included between the tapering sides of the job when extended to meet at a point.
Knurling
Knurling is a manufacturing process, typically conducted on a lathe, whereby a pattern of straight, angled or crossed lines is cut or rolled into the material.
The operation is performed for producing indentations on a part of a workpiece. Knurling allows hands or fingers to get a better grip on the knurled object than would be provided by the originally smooth metal surface. Occasionally, the knurled pattern is a series of straight ridges or a helix of "straight" ridges rather than the more-usual crisscross pattern.
Diamond Knurling
A hybrid of Annular Rings and Linear Knurling in which a diamond shape is formed. It is used to provide better grip on components, and is the most common type used on everyday objects.
Facing
Facing is the process of removing metal from the end of a workpiece to produce a flat surface. Most often, the workpiece is cylindrical, but using a 4-jaw chuck you can face rectangular or odd-shaped work to form cubes and other non-cylindrical shapes.
When a lathe cutting tool removes metal it applies considerable tangential (i.e. lateral or sideways) force to the workpiece. To safely perform a facing operation the end of the workpiece must be positioned close to the jaws of the chuck. The workpiece should not extend more than 2-3 times its diameter from the chuck jaws unless a steady rest is used to support the free end.
Grooving
Grooving is like parting, except that grooves are cut to a specific depth instead of severing a completed/part-complete component from the stock. Grooving can be performed on internal and external surfaces, as well as on the face of the part (face grooving or trepanning).
Chamfering
Chamfering is the operation of beveling the extreme end of a workpiece. This is done to remove the burrs, to protect the end of the workpiece from being damaged and to have a better look. The operation may be performed after knurling, rough turning, boring, drilling. Chamfering is an essential operation before thread cutting so that the nut may pass freely on the threaded workpiece.
Refrences:
Turning Process, Defects, Equipment. 2016.[ONLINE] Available at: http://www.custompartnet.com/wu/turning. [Accessed 05 December 2015].
Lathe Machine Operations – Chamfering & Parting off – Education Portal. 2016. [ONLINE] Available at: http://www.educationportals.net/lathe-machine-operations-chamfering-parting-off/. [Accessed 05 December 2015].
The Centre Lathe - Facing Off. 2016. [ONLINE] Available at: http://www.technologystudent.com/equip1/mlathe2.htm. [Accessed 05 December 2015]
Cutting Tool Applications, Chapter 6: Grooving and Threading. 2016. [ONLINE] Available at: http://americanmachinist.com/cutting-tools/cutting-tool-applications-chapter-6-grooving-and-threading. [Accessed 05 December 2015]
Special Operations on the Lathe | smithy.com. 2016.| smithy.com. [ONLINE] Available at: http://www.smithy.com/machining-handbook/chapter-3/page/25. [Accessed 05 December 2015].