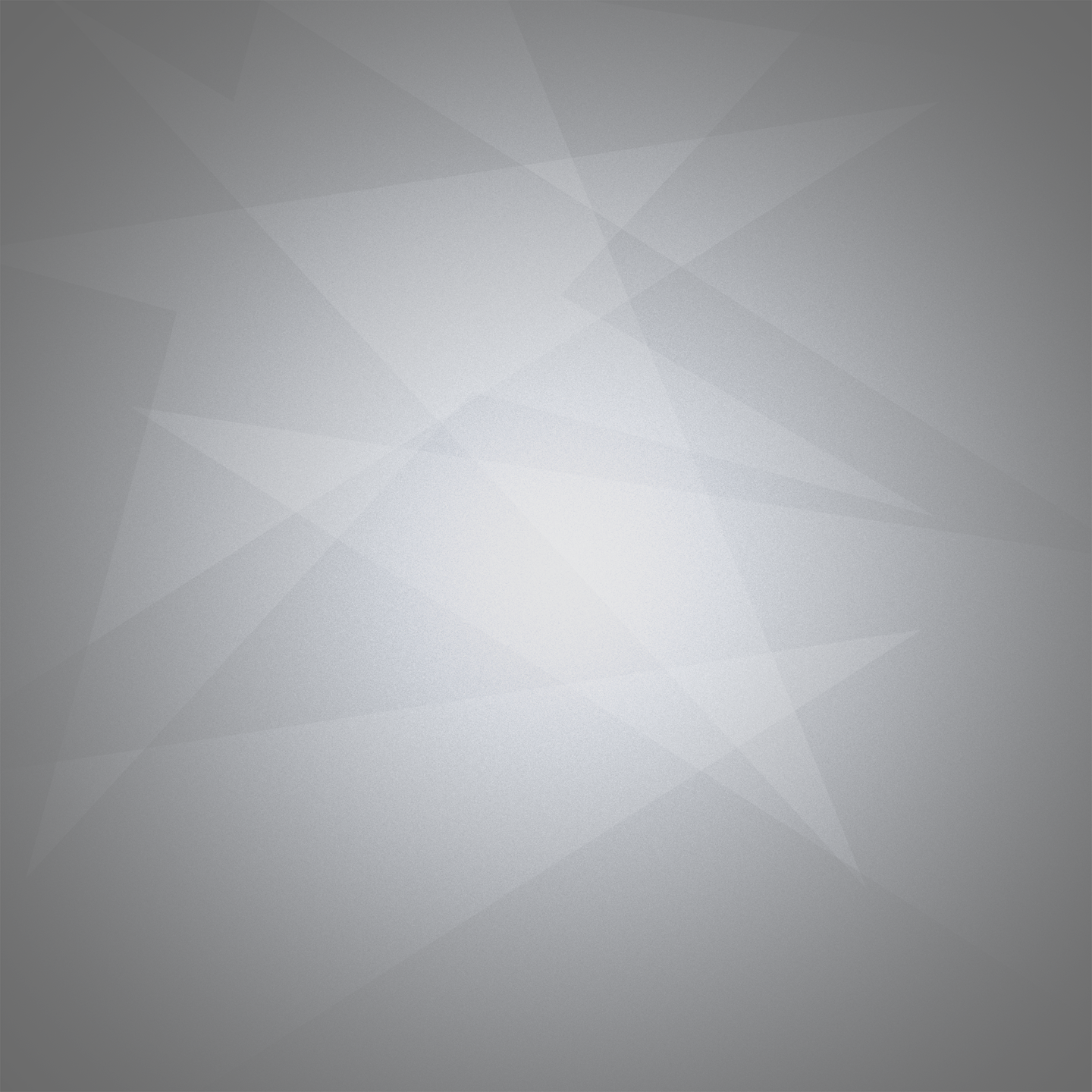

Engineering Applications
AME-5001
Group - II
Taper turning
What is taper turning?
When the diameter of a piece changes uniformly, from one end to the other, the piece is said to be tapered. Taper turning as a machining operation is the gradual reduction in diameter from one part of a cylindrical workpiece to another part.
In ordinary straight turning, the cutting tool moves along a line parallel to the axis of the work, causing the finished job to be the same diameter throughout. However, when cutting a taper, the tool moves at an angle to the axis of the work, producing a taper.
Methods of taper turning
The basic principle behind turning a taper is that, the work must either be mounted in a lathe so that the axis upon which it turns is at an angle to the axis of the lathe, or cause the cutting tool to move at an angle to the axis of the lathe.
The method used for turning a taper depends on the degree, length, location of the taper. The three basic methods of turning a taper require the operator to use either a compound rest, offset the tailstock, or use the taper attachment. With any of these methods, the cutting tool must be set exactly on centre with the axis of the workpiece or the workpiece will not be truly conical, and the rate of taper will vary with each cut.
Taper Turning Attachment
The taper attachment is used for turning and boring tapers. It is bolted to the back of the carriage saddle. In operation, it is connected to the cross-slide so that it moves the cross-slide laterally as the carriage moves longitudinally.
This action causes the cutting tool to move at an angle to the axis of the workpiece to produce a taper.
The angle of the desired taper is set on the guide bar of the attachment, and the guide bar support is clamped to the lathe bed. Since the cross-slide is connected to a shoe that slides on this guide bar, the tool follows along a line that is parallel to the guide bar and hence at an angle to the workpiece axis corresponding to the desired taper.
Compound Rest
The compound rest is generally used for turning or boring short steep tapers, but it can also be used for longer, gradual tapers, providing the length of the taper does not exceed the distance the compound rest will move upon its slide.
This method can be used with a high degree of accuracy, but is
Somewhat limited due to the lack of an automatic feed and the length of the taper being restricted to the movement of the slide.
The compound rest base is graduated in degrees and can be set at the required angle for taper turning or boring.
With this method, it is necessary to know the included angle of the taper to be machined.
An included angle is formed by and between two intersecting straight lines.)
The angle of the taper with the centerline is one-half the included angle and will be the angle that the compound rest is set for.
For example: To true up a lathe center which has an included angle of 60◦, the compound rest would be set at 30◦ from parallel to the ways.
If the taper is given in taper inches per foot, the angle for the compound rest setting will have to be computed or taken from an appropriate taper sizes and angles table.
OFF SETTING THE TAILSTOCK
The tailstock offset method is generally used to cut a taper when no taper attachment
is available. This involves moving the tailstock centre out-of-line with the headstock
Centre.
However, the amount that the tailstock may be offset is limited. This method
will not permit steep tapers to be turned or standard tapers to be turned on the end of
a long piece of work.
Since the work will be essentially at an angle it will need to be
Machined between centers. Thus, a chuck or collet cannot be used to hold the
Workpiece. Great care must be exercised in setting the tailstock back to centre when
the taper turning operation is completed.
Knurling
A knurl is a raised impression on the surface of the work piece produced by two hardened rolls and is usually one of two patterns: diamond or straight (Figure I-275). The diamond pattern is formed by a right-hand and a left-hand helix mounted in a self-centering head.
The straight pattern is formed by two straight rolls. These common knurl patterns can be fine, medium, or coarse. Diamond knurling is used to improve the appearance of a part and to provide a good gripping surface for levers and tool handles. Straight knurling is used to increase the size of a part for press fits in light-duty applications. A disadvantage to this use of knurls is that the fit has less contact area than
a standard fit.
Three basic types of knurling tool holders are used:
The knuckle-joint holder (Figure I-276), the revolving head holder (Figure I-277), and the straddle holder (Figure I-278). The straddle holder allows small diameters to be knurled with less distortion. This principle is used for knurling on production machines.
Knurling works best on workpieces mounted between centers. When held in a chuck and supported by a center, the workpiece tends to crawl back into the chuck and out of the supporting center with the high pressure of the knurl.
This is especially true when the knurl is started at the tailstock end and the feed is toward the chuck. Long, slender pieces push away from the knurl and will stay bent if the knurl is left in the work after the lathe is stopped. Knurls do not cut but displace the metal with high pressure. Lubrication is more important than cooling, so a cutting oil or lubricating oil is satisfactory. Low speeds (about the same as for threading) and a feed of about .010 to .015 in. are used for knurling.
References
Lathes and Types of Lathes. 2015. [ONLINE] Available at: http://www.longwood.edu/assets/chemphys/CH7.PDF. [Accessed 05 December 2015].
Lathe Parts Page 1. 2015. [ONLINE] Available at: http://www.lathes.co.uk/latheparts/. [Accessed 05 December 2015].
How To Use a Lathe. 2015. [ONLINE] Available at: http://www.americanmachinetools.com/how_to_use_a_lathe.htm. [Accessed 05 December 2015].
Taper turning methods | Classle. 2015. [ONLINE] Available at: https://www.classle.net/book/taper-turning-methods. [Accessed 05 December 2015]
Using a Taper Attachment, How?. 2015. [ONLINE] Available at: http://www.practicalmachinist.com/vb/general/using-taper-attachment-how-197549/. [Accessed 05 December 2015].
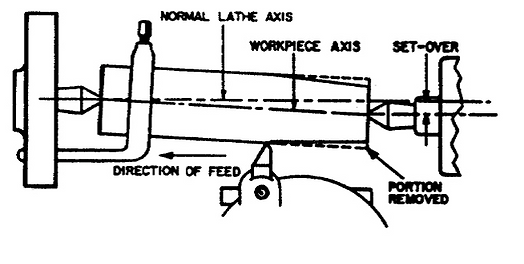
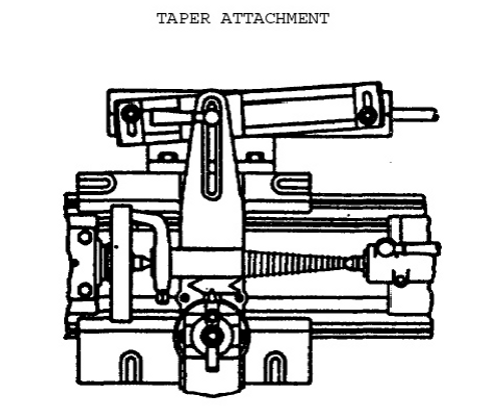

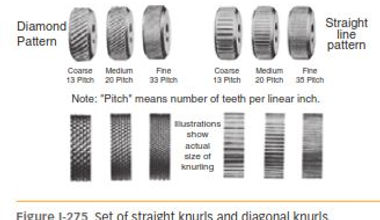
