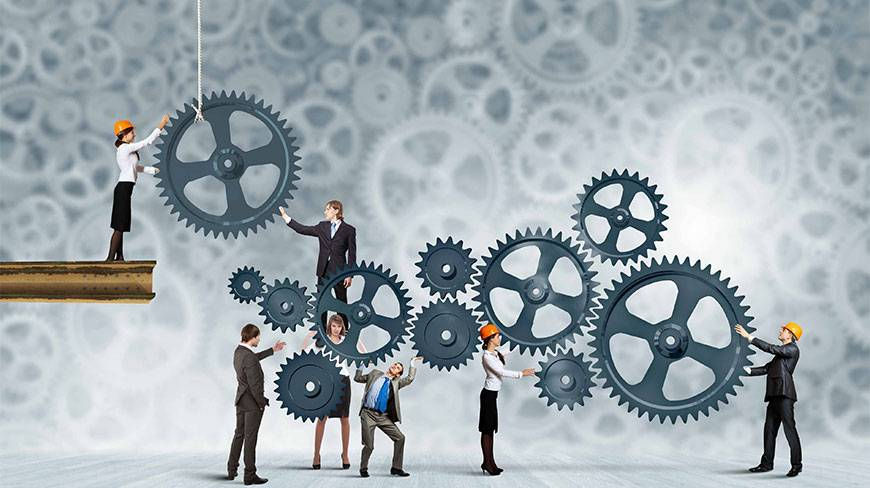

Automatic Can-Crusher
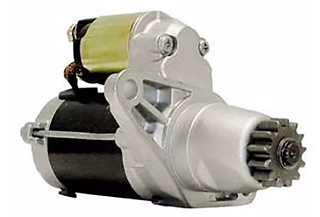
Preliminary Process
Prior to the process of manufacturing, the selection of motor, pulley and flywheel was done by the production manager. The selected motor was a starter motor of Toyota Camry. The selected piston and flywheel were also parts of a car engine.
First Welding
Once the selection was done, the flywheel was welded to the starter motor's shaft. The piston rod was also elongated by welding a steel rod to it.
The body frame was manufactured by welding cut out pieces of hollow mild steel bars accroding to the 3D - design. The welding process was done in a workshop outside the campus.

Drilling
Drilling was done on the flywheel to make the hole for screw connecting the piston larger. The process was carried out inside the campus by the team members.
Replacing the Previous Motor
The first motor (starter motor) used for the project proved to be a wrong selection because it only had very high RPM with least torque. Therefore, enough force was not generated byt the motor to crush the can. In order to rectify this, the starter motor was replaced by a car windshield wiper motor. The reason of selecting this motor was because it had high torque with the required amount of RPM. The first motor was thus removed and the new motor's shaft was welded to the flywheel.